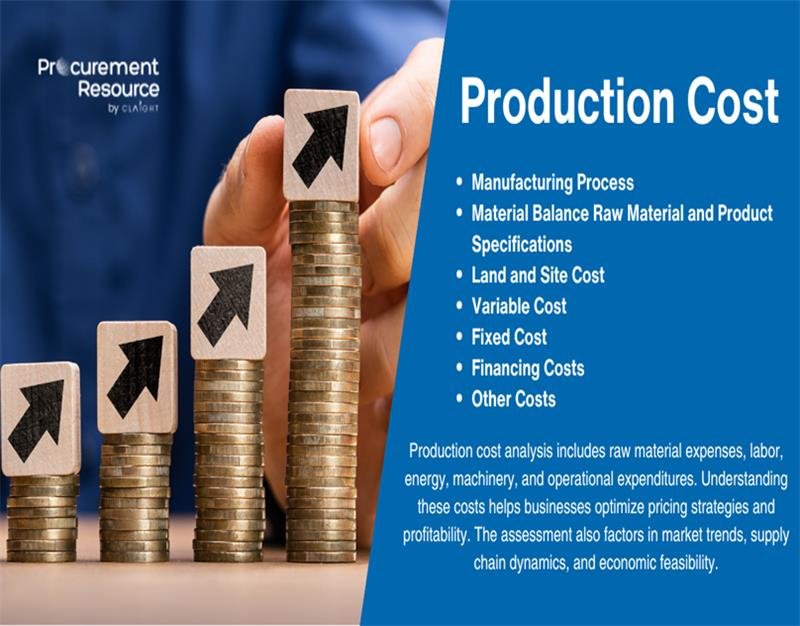
Ethylene Acrylic Elastomer (AEM) is a high-performance synthetic rubber known for its exceptional resistance to heat, oil, and oxidation, making it highly valuable in automotive and industrial applications. As industries continue to demand durable elastomers for components like hoses, seals, and gaskets, understanding the Ethylene Acrylic Elastomer Production Cost becomes essential for manufacturers, procurement professionals, and investors. This article presents a detailed cost analysis report, including labor, logistics, utilities, raw materials, manufacturing process, and market insights, to help businesses optimize sourcing and production strategies.
Product Overview: Ethylene Acrylic Elastomer
Ethylene Acrylic Elastomers are terpolymers composed of ethylene, acrylic ester, and a cure-site monomer. These elastomers are particularly used in automotive transmissions and under-the-hood components due to their thermal stability, flexibility, and resistance to automotive fluids. AEM also offers outstanding vibration dampening and aging properties.
The production process of AEM involves emulsion polymerization, followed by compounding and vulcanization. Each stage of the manufacturing chain has cost implications, which are analyzed in detail below.
Extensive Ethylene Acrylic Elastomer Production Cost Analysis Report
An Ethylene Acrylic Elastomer Production Cost Analysis Report provides a granular view of every cost component in the value chain. These cost drivers are critical for businesses aiming to understand their operational expenditure or evaluate potential investments in AEM production.
1. Raw Material Costs
The primary raw materials required for AEM production are:
- Ethylene
- Acrylic acid or its esters (like methyl acrylate)
- Cure-site monomers (typically containing carboxylic acid groups or halogens)
Fluctuations in the prices of ethylene and acrylic esters—mainly derived from petroleum feedstocks—heavily influence the overall cost structure.
2. Labor Charges
Labor costs vary across manufacturing regions depending on the wage structures and skill levels. Labor includes plant operators, technical staff, maintenance crew, and quality control personnel.
3. Utilities
Production of AEM involves high-temperature polymerization and subsequent thermal processing. Utility costs include:
- Electricity for mixing and polymerization
- Steam for heating
- Water for cooling
- Compressed air for automation systems
These utilities form a considerable share of variable costs, especially in high-throughput plants.
4. Logistics and Supply Chain
Transportation of hazardous raw materials and finished elastomers requires careful logistical planning. Costs here include:
- Bulk shipping of ethylene and acrylic esters
- Cold storage and handling for heat-sensitive materials
- Finished product delivery to OEMs and downstream converters
Efficient supply chain management minimizes delays and inventory holding costs.
5. Manufacturing Process
The process flow for AEM includes:
- Emulsion polymerization using surfactants and initiators
- Post-treatment processes like coagulation, washing, and drying
- Compounding with additives and fillers
- Vulcanization using peroxides or other curing agents
Each step incurs equipment, labor, and utility expenses, which are consolidated in the production cost structure.
6. Pre-feasibility and Industrial Trends
Before setting up a manufacturing plant, pre-feasibility assessments are crucial. These studies consider:
- Capital expenditure (CAPEX) for plant setup
- Regulatory compliance costs
- Expected return on investment
- Regional industrial trends like automotive growth or emission regulations
Ethylene acrylic elastomer production is capital-intensive, and cost forecasting helps in investment decision-making.
Market and Industrial Trends
The global demand for AEM is expanding, largely driven by the automotive, construction, and appliance sectors. Several industrial trends are shaping the market:
- Rising Demand for Heat-Resistant Materials: Automakers are increasingly using AEM in turbocharged engines and high-heat applications.
- Environmental Regulations: Stricter fuel efficiency and emission norms push for advanced elastomer materials.
- Substitute Analysis: While Fluoroelastomers and NBR are alternatives, AEM strikes a balance between performance and cost, increasing its adoption.
Procurement Resource provides market analysis tools and cost modeling support, helping organizations respond to these trends proactively.
Regional Cost Differentiation
Production costs for Ethylene Acrylic Elastomer vary across regions due to differences in:
- Raw material access (e.g., North America has easy access to shale-based ethylene)
- Labor rates (lower in APAC regions)
- Environmental regulations (stricter in EU, adding compliance costs)
- Infrastructure availability
For example:
- North America: Benefit from raw material availability but face moderate labor and compliance costs.
- Asia-Pacific (APAC): Lower production costs due to inexpensive labor and growing domestic demand.
- Europe: High energy prices and stringent regulations increase the overall cost of production.
This regional analysis aids manufacturers in location-based feasibility studies and supplier evaluations.
Supply Chain Optimization and Procurement Insights
Efficient procurement is essential for managing the overall production cost. Strategic sourcing of raw materials like ethylene and acrylates, bulk purchasing, and long-term supplier contracts can significantly lower material input costs.
Procurement Resource supports manufacturers and buyers with:
- Price monitoring and forecasting
- Supplier evaluation tools
- Negotiation support based on cost models
- Risk management strategies for volatile input costs
By leveraging cost analysis and market intelligence, companies can strengthen their supply chain resilience and cost-efficiency.
Cost Modeling and Forecast Tools
A well-structured cost model is essential for budgeting, product pricing, and business planning. Cost modeling for AEM includes:
- Fixed and variable cost segregation
- Scenario analysis for raw material price changes
- Capacity-based scaling for economies of scale
- Margin forecasting under different market conditions
Advanced digital dashboards and interactive models help stakeholders simulate various pricing and cost scenarios. These insights are invaluable for CFOs, procurement heads, and production planners.
Request a Free Sample
To gain a better understanding of the production economics and market dynamics of Ethylene Acrylic Elastomer, businesses can access a free sample report.
Request a Free Sample-
This report provides:
- Cost breakdown by region and plant capacity
- Manufacturing process overview
- Market trends and forecasts
- Pre-feasibility insights for new entrants
Stay informed with real-time updates and accurate market data delivered by Procurement Resource experts.
Connect With Us
To stay updated with the latest market trends and detailed production cost reports, connect with us on social media or get in touch directly:
Contact Information
Company Name: Procurement Resource
Contact Person: Ashish Sharma (Sales Representative)
Email: sales@procurementresource.com
Location: 30 North Gould Street, Sheridan, WY 82801, USA
Phone Numbers:
UK: +44 7537171117
USA: +1 307 363 1045
Asia-Pacific (APAC): +91 1203185500
Connect With Us Online:
X:-https://x.com/procurementres
LinkedIn:-https://www.linkedin.com/company/procurement-resource-official/
Pinterest:-https://www.pinterest.com/procurementresource/
YouTube:-https://www.youtube.com/@procurementresource
Website:-https://www.procurementresource.com/